Mercury Motion was established in 2009. It is a high-tech enterprise integrating R&D, production and sales of various coreless motor sizes,coreless motor speed controller,coreless motor drone,coreless motor size 408,coreless motor speed control.Products are widely used in cars, medical equipment, intelligent security, household appliances, western kitchen equipment, machinery and electronics and other high-end transmission structures, products are exported to more than 50 countries and regions at home and abroad.It has accumulated more than ten years of successful cases experience in the motor field, providing customers with perfect overall transmission mechanism solutions.
Product name
| coreless motor speed control
| Keyword
| coreless motor sizes,coreless motor speed controller,coreless motor drone,coreless motor size 408,coreless motor speed control
| Place of Origin | China | Rated
| DC 5V
| Type
| GEAR MOTOR
| Total length
| 69.8-60mm, (Contact us for specific information to confirm)
| Applicable Industries
| household appliances, etc.
| Weight
| 5kg
| Product Description
| A gear motor is a type of motor that incorporates gears into its design to achieve a specific speed and torque output. It typically consists of a motor, a gearbox, and a series of gears that work together to control the motor's speed and power.
| Life span
| 18 years (Contact us for specific information to confirm)
| Advantage
| We keep good quality and competitive price to ensure our customers benefit
| Packing
| 131x145x93mm(Contact us for specific information to confirm)
| Sales country
| All over the world for example:Suriname,Burundi,Guatemala,Namibia,Coral Sea Islands,Pakistan,Montserrat,Monaco
| Certification
| ISO9001
| color
| black/grey
| MOQ
| 49pcs(Contact us for specific information to confirm)
|
Please contact us for details about Precision Motors
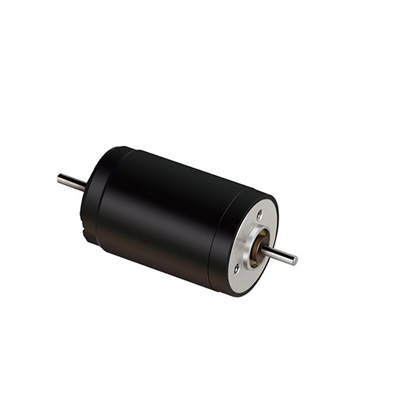
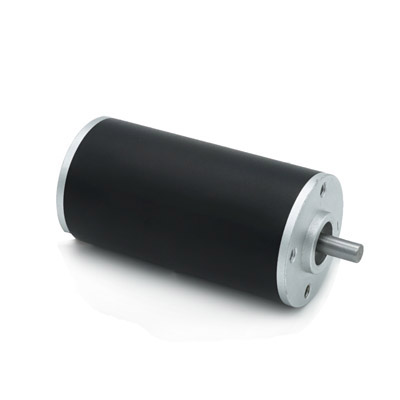
For more information about GM Planetary Gear Motors, please contact us. 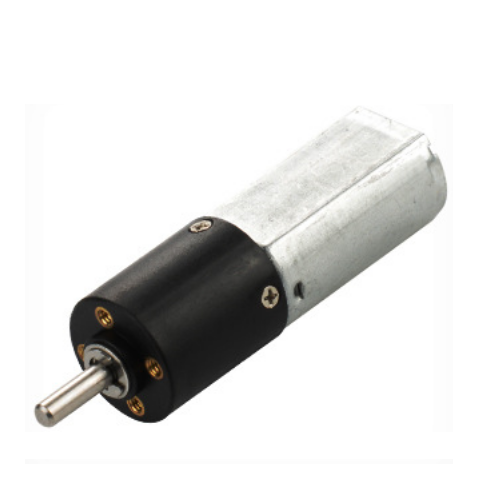
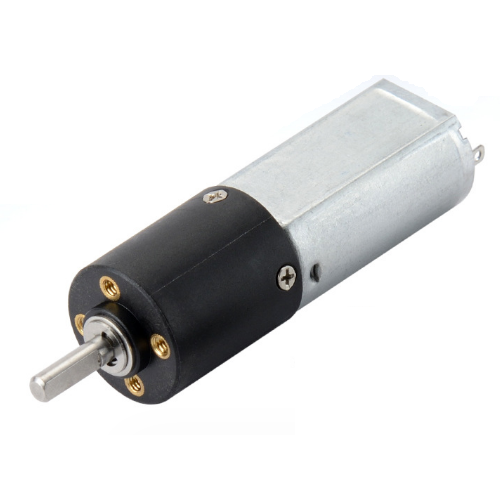
Please contact us for details about Spur Gear Motors 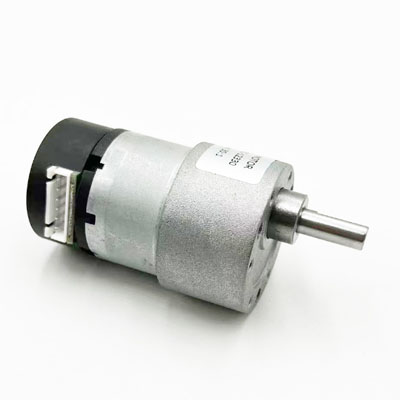
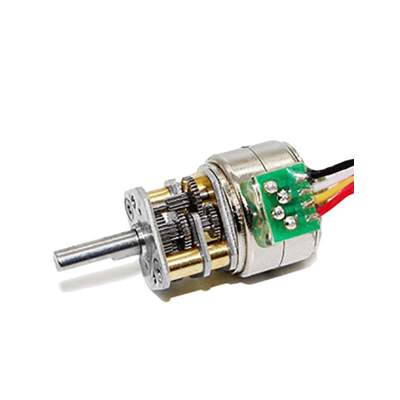
coreless motor speed control services FAQs Guide
Are you looking for a quick review guide about coreless motor speed controlservices?
An ultimate FAQ buying guide is available to help you.This guide contains all the information about all the important facts, figures, and various processes regarding coreless motor speed control services.
Let’s continue!
1.How do you troubleshoot common issues with gear motors? 2.What are the power requirements for a gear motor? 3.How does a gear motor compare to other types of motors? 4.How durable are gear motors and what is their expected lifespan? 5.Can gear motors be used in precision applications? 6.How does the size of a gear motor affect its performance? 7.What types of bearings are typically used in gear motors? 8.How does the gear design affect the performance of a gear motor? 9.Can gear motors handle varying load demands? 10.Is it possible to increase the torque of a gear motor? 1.How do you troubleshoot common issues with gear motors? We continue to improve coreless motor speed control products and processes to improve efficiency. 1. Check the power supply: Make sure the gear motor is receiving the correct voltage and that the power supply is functioning properly.
2. Inspect the wiring: Check for loose or damaged wires, and make sure they are connected to the correct terminals.
3. Check for mechanical obstructions: Make sure there are no obstructions preventing the gear motor from turning, such as debris or misaligned gears.
4. Lubricate the gears: If the gear motor is making unusual noises or is not turning smoothly, it may need to be lubricated. Use a suitable lubricant according to the manufacturer's recommendations.
5. Check for overheating: If the gear motor feels hot to the touch, it may be overheating. This could be due to a faulty motor or excessive load on the motor. Reduce the load or replace the motor if necessary.
6. Test the motor with a multimeter: Use a multimeter to check the voltage and current of the gear motor. This can help identify any electrical issues.
7. Inspect the motor brushes: If the gear motor has carbon brushes, check them for wear and replace if necessary.
8. Check the motor bearings: If the gear motor has bearings, check them for wear and replace if necessary.
9. Consult the manufacturer's manual: If the gear motor is still not functioning properly, refer to the manufacturer's manual for troubleshooting tips specific to your model.
10. Seek professional help: If you are unable to identify or fix the issue, it may be best to seek help from a professional technician or contact the manufacturer for assistance. 2.What are the power requirements for a gear motor? I have a comprehensive after -sales service system, which can pay attention to market trends in time and adjust our strategy in a timely manner. The power requirements for a gear motor depend on several factors, including the size and type of motor, the gear ratio, and the load being driven. Generally, gear motors require a power supply with a voltage and current rating that is compatible with the motor's specifications. The power requirements can range from a few watts for small gear motors to several kilowatts for larger ones. It is important to consult the manufacturer's specifications for the specific gear motor being used to determine its power requirements. 3.How does a gear motor compare to other types of motors? We focus on innovation and continuous improvement to maintain a competitive advantage. A gear motor is a type of motor that combines a motor and a gearbox into one unit. This allows for increased torque and reduced speed, making it suitable for applications that require high torque and low speed, such as in industrial machinery, robotics, and automotive systems.
Compared to other types of motors, such as DC motors, AC motors, and stepper motors, gear motors have the following advantages:
1. High torque: Gear motors have a higher torque output compared to other types of motors, making them suitable for heavy-duty applications.
2. Precise speed control: The gearbox in a gear motor allows for precise speed control, making it ideal for applications that require a specific speed.
3. Compact size: Gear motors are compact in size, making them suitable for applications where space is limited.
4. Low maintenance: The gearbox in a gear motor helps to reduce wear and tear on the motor, resulting in lower maintenance requirements.
5. Cost-effective: Gear motors are generally more cost-effective compared to other types of motors, making them a popular choice for many applications.
4.How durable are gear motors and what is their expected lifespan? We have a professional team that is committed to the innovation and development of coreless motor speed control. The durability of gear motors can vary depending on the quality of the motor and the conditions in which it is used. Generally, gear motors are designed to be durable and have a long lifespan. They are often used in industrial and commercial applications where they are subjected to heavy use and harsh environments.
The expected lifespan of a gear motor can range from 5 to 20 years, depending on the type of motor and its usage. Factors that can affect the lifespan of a gear motor include the quality of the materials used, the maintenance and care of the motor, and the load and speed at which it is operated.
Some gear motors may also come with a warranty that guarantees a certain lifespan. It is important to follow the manufacturer's recommendations for maintenance and usage to ensure the longest possible lifespan for your gear motor. 5.Can gear motors be used in precision applications? We actively participate in the coreless motor speed control industry associations and organization activities. The corporate social responsibility performed well, and the focus of brand building and promotion
Yes, gear motors can be used in precision applications. They are commonly used in applications that require precise control of speed, torque, and position, such as robotics, CNC machines, and medical equipment. Gear motors offer high torque and low speed capabilities, making them suitable for precise movements and positioning. Additionally, they can be combined with encoders and other feedback devices to further enhance their precision and accuracy. 6.How does the size of a gear motor affect its performance? We focus on providing high coreless motor speed control quality products and services.
The size of a gear motor can affect its performance in several ways:
1. Torque: The size of the gear motor directly affects the amount of torque it can produce. A larger gear motor will have a larger gear ratio, which means it can produce more torque. This is important for applications that require high torque, such as lifting heavy loads.
2. Speed: The size of the gear motor also affects its speed. A larger gear motor will have a slower speed due to the larger gear ratio. This is important for applications that require precise and slow movements, such as in robotics.
3. Power: The size of the gear motor also affects its power output. A larger gear motor will have a higher power output due to the larger gear ratio and larger motor size. This is important for applications that require high power, such as in industrial machinery.
4. Efficiency: The size of the gear motor can also affect its efficiency. A larger gear motor may have a higher efficiency due to the larger gear ratio, which reduces the amount of energy lost in the gear train. However, this also depends on the quality and design of the gear motor.
5. Durability: The size of the gear motor can also affect its durability. A larger gear motor may be more durable due to the larger size and stronger components. This is important for applications that require frequent and heavy use.
Overall, the size of a gear motor plays a crucial role in its performance and should be carefully considered when selecting a motor for a specific application. 7.What types of bearings are typically used in gear motors? We adhere to the principle of integrity and transparency, and establish long -term relationships with partners, and we attach great importance to this detail. 1. Ball bearings: These are the most common type of bearings used in gear motors. They consist of a series of balls held in place by a cage, which allows for smooth rotation and reduced friction.
2. Roller bearings: These bearings use cylindrical rollers instead of balls to reduce friction and support heavy loads. They are commonly used in high-speed gear motors.
3. Tapered roller bearings: These bearings have tapered rollers that are designed to handle both radial and axial loads. They are commonly used in gear motors that require high precision and durability.
4. Needle bearings: These bearings use long, thin rollers to support heavy loads and reduce friction. They are commonly used in gear motors with limited space.
5. Thrust bearings: These bearings are designed to handle axial loads and are commonly used in gear motors that require high thrust capacity.
6. Spherical roller bearings: These bearings have a spherical outer raceway, which allows for misalignment and can handle heavy radial loads. They are commonly used in gear motors that operate at high speeds.
7. Cylindrical roller bearings: These bearings use cylindrical rollers to support heavy radial loads and are commonly used in gear motors with high radial load requirements.
8. Bushings: These are simple bearings that consist of a smooth cylindrical or spherical surface that allows for rotation with minimal friction. They are commonly used in low-speed gear motors.
9. Plain bearings: These bearings have a smooth surface that allows for sliding motion and are commonly used in gear motors that require low friction and high precision.
10. Magnetic bearings: These bearings use magnetic fields to support the rotating shaft and eliminate the need for physical contact. They are commonly used in high-speed gear motors that require low friction and high precision. 8.How does the gear design affect the performance of a gear motor? We have a first -class management team, and we pay attention to teamwork to achieve common goals. The gear design plays a crucial role in determining the performance of a gear motor. Some of the ways in which the gear design affects the performance are:
1. Speed and Torque: The gear design determines the speed and torque output of the gear motor. A gear motor with a higher gear ratio will have a lower speed but higher torque output, while a gear motor with a lower gear ratio will have a higher speed but lower torque output.
2. Efficiency: The gear design also affects the efficiency of the gear motor. A well-designed gear system can minimize friction and maximize power transfer, resulting in higher efficiency.
3. Noise and Vibration: The gear design can also impact the noise and vibration levels of the gear motor. A poorly designed gear system can produce excessive noise and vibration, leading to reduced performance and increased wear and tear.
4. Load Capacity: The gear design also determines the load capacity of the gear motor. A gear motor with a robust and well-designed gear system can handle heavier loads without compromising its performance.
5. Durability: The gear design can also affect the durability of the gear motor. A well-designed gear system can withstand high levels of stress and wear, resulting in a longer lifespan for the gear motor.
Overall, the gear design is a critical factor in determining the performance, efficiency, and durability of a gear motor. A well-designed gear system can significantly improve the overall performance of the gear motor, while a poorly designed one can lead to various issues and reduce its effectiveness. 9.Can gear motors handle varying load demands? We have been working hard to improve service quality and meet customer needs. Yes, gear motors are designed to handle varying load demands. The gear ratio of the motor allows it to provide the necessary torque to handle different load demands. Additionally, some gear motors have adjustable speed and torque settings, making them even more versatile in handling varying load demands. 10.Is it possible to increase the torque of a gear motor? We continuously upgrade our skills and knowledge to adapt to changing coreless motor speed control market needs. Yes, it is possible to increase the torque of a gear motor by using a larger gear ratio, increasing the voltage or current supplied to the motor, or by using a more powerful motor with higher torque capabilities. Additionally, optimizing the design and materials of the gears and motor can also help to increase the torque output.
|