Founded in 2009,Mercury Motion specializes in high end micro motors, such as brushless motors, gear motors, stepper motors…etc.Especially the precision gear motors, we could design and produce all the gears and we have a full production line of CNC center .This combination makes us have the unique advantage of the gear motors industry. Our motors are widely used in cars, home appliances,medical equipment, electrical devices, ATMs and robots, etc.
Currently, our company is exported to America, Ukraine,Juan de Nova Island,Kazakhstan,Tokelau,Timor-Leste,Tuvalu and other more than 50 countries and regions. Mercury Motion company has a strong technical team, a wealth of experience in field service, and effectively provide the right solutions and cost-effective products for customers, We are adhering to the concept credibility first
Product name
| coreless motor sizes
| Keyword
| coreless motor speed control,coreless motor gears,coreless motor speed controller,coreless motor gearbox,coreless motor drone,coreless motor size 408,coreless motor inside,coreless motor sizes
| Place of Origin | China | Rated
| DC 5V
| Type
| GEAR MOTOR
| Total length
| 72.8-44.1mm, (Contact us for specific information to confirm)
| Applicable Industries
| health industry, etc.
| Weight
| 14kg
| Product Description
| A gear motor is a type of motor that incorporates gears into its design to achieve a specific speed and torque output. It typically consists of a motor, a gearbox, and a series of gears that work together to control the motor's speed and power.
| Life span
| 12 years (Contact us for specific information to confirm)
| Advantage
| We keep good quality and competitive price to ensure our customers benefit
| Packing
| 118x113x123mm(Contact us for specific information to confirm)
| Sales country
| All over the world for example:Ukraine,Juan de Nova Island,Kazakhstan,Tokelau,Timor-Leste,Tuvalu
| MOQ
| 41pcs(Contact us for specific information to confirm)
|
Please contact us for details about Precision Motors
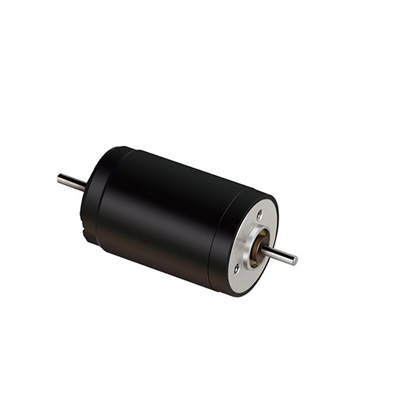
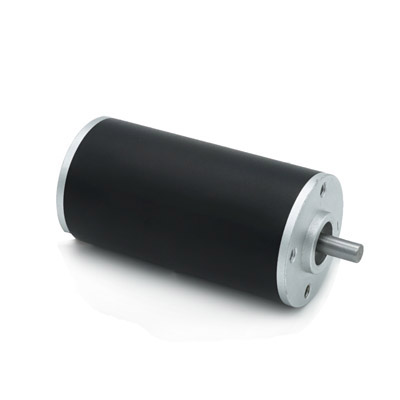
For more information about GM Planetary Gear Motors, please contact us. 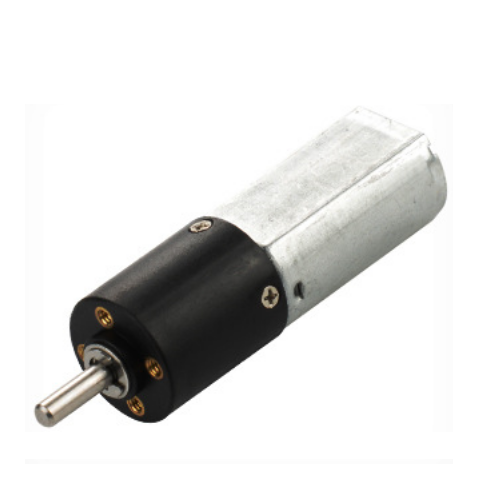
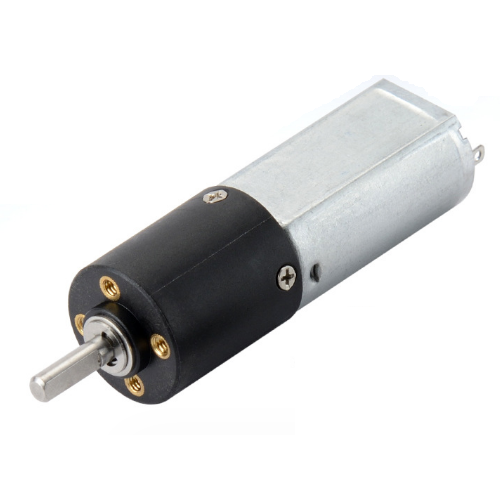
Please contact us for details about Spur Gear Motors 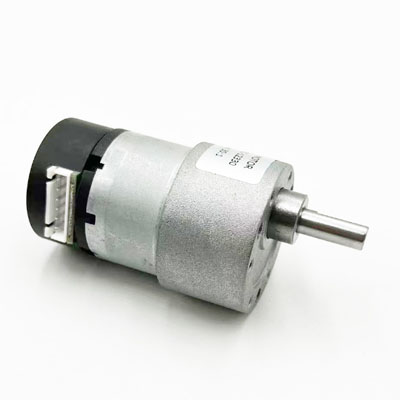
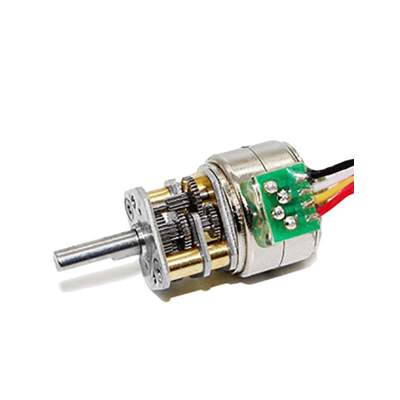
coreless motor sizes services FAQs Guide
Are you looking for a quick review guide about coreless motor sizesservices?
An ultimate FAQ buying guide is available to help you.This guide contains all the information about all the important facts, figures, and various processes regarding coreless motor sizes services.
Let’s continue!
1.Are gear motors energy efficient? 2.How do you troubleshoot common issues with gear motors? 3.How durable are gear motors and what is their expected lifespan? 4.How do you ensure proper installation of a gear motor? 5.How does a gear motor compare to other types of motors? 6.What are the operating temperature ranges for gear motors? 7.What are the differences between helical, spur, and planetary gear motors? 8.What are the advantages of a gear motor? 9.What controls are necessary for operating a gear motor? 10.What are the differences between AC and DC gear motors? 1.Are gear motors energy efficient? We are centered on customers and always pay attention to customers' needs for coreless motor sizes products. Yes, gear motors are generally considered to be energy efficient. This is because they use gears to reduce the speed of the motor while increasing the torque, allowing them to operate at a lower speed and use less energy. Additionally, gear motors are often designed with high-quality bearings and efficient motor designs to further improve their energy efficiency. 2.How do you troubleshoot common issues with gear motors? We continue to improve coreless motor sizes products and processes to improve efficiency. 1. Check the power supply: Make sure the gear motor is receiving the correct voltage and that the power supply is functioning properly.
2. Inspect the wiring: Check for loose or damaged wires, and make sure they are connected to the correct terminals.
3. Check for mechanical obstructions: Make sure there are no obstructions preventing the gear motor from turning, such as debris or misaligned gears.
4. Lubricate the gears: If the gear motor is making unusual noises or is not turning smoothly, it may need to be lubricated. Use a suitable lubricant according to the manufacturer's recommendations.
5. Check for overheating: If the gear motor feels hot to the touch, it may be overheating. This could be due to a faulty motor or excessive load on the motor. Reduce the load or replace the motor if necessary.
6. Test the motor with a multimeter: Use a multimeter to check the voltage and current of the gear motor. This can help identify any electrical issues.
7. Inspect the motor brushes: If the gear motor has carbon brushes, check them for wear and replace if necessary.
8. Check the motor bearings: If the gear motor has bearings, check them for wear and replace if necessary.
9. Consult the manufacturer's manual: If the gear motor is still not functioning properly, refer to the manufacturer's manual for troubleshooting tips specific to your model.
10. Seek professional help: If you are unable to identify or fix the issue, it may be best to seek help from a professional technician or contact the manufacturer for assistance. 3.How durable are gear motors and what is their expected lifespan? We have a professional team that is committed to the innovation and development of coreless motor sizes. The durability of gear motors can vary depending on the quality of the motor and the conditions in which it is used. Generally, gear motors are designed to be durable and have a long lifespan. They are often used in industrial and commercial applications where they are subjected to heavy use and harsh environments.
The expected lifespan of a gear motor can range from 5 to 20 years, depending on the type of motor and its usage. Factors that can affect the lifespan of a gear motor include the quality of the materials used, the maintenance and care of the motor, and the load and speed at which it is operated.
Some gear motors may also come with a warranty that guarantees a certain lifespan. It is important to follow the manufacturer's recommendations for maintenance and usage to ensure the longest possible lifespan for your gear motor. 4.How do you ensure proper installation of a gear motor? We have advantages in marketing and channel expansion. Suppliers have established good cooperative relations, continuously improved workflows, improved efficiency and productivity, and provided customers with high -quality products and services. 1. Read the manufacturer's instructions: The first step to ensuring proper installation of a gear motor is to carefully read and understand the manufacturer's instructions. This will provide you with important information such as the correct mounting position, torque specifications, and any special tools or techniques required for installation.
2. Choose the right mounting position: The gear motor should be mounted in a position that allows for proper alignment with the driven equipment. It should also be mounted in a location that provides adequate ventilation and protection from external elements.
3. Check for proper alignment: Before installing the gear motor, make sure that the shafts of the motor and the driven equipment are properly aligned. Misalignment can cause excessive wear and damage to the gear motor.
4. Use the correct mounting hardware: Make sure to use the correct mounting hardware provided by the manufacturer. This will ensure that the gear motor is securely attached to the mounting surface and prevent any vibrations or movement during operation.
5. Apply the correct torque: It is important to use a torque wrench to tighten the mounting bolts to the specified torque. Over-tightening can damage the gear motor, while under-tightening can cause the motor to become loose and affect its performance.
6. Check for proper lubrication: Before starting the gear motor, make sure that all moving parts are properly lubricated. This will ensure smooth operation and prevent premature wear and tear.
7. Test the motor: Once the gear motor is installed, test it to ensure that it is functioning properly. Check for any unusual noises or vibrations and make any necessary adjustments.
8. Regular maintenance: To ensure the longevity and proper functioning of the gear motor, it is important to perform regular maintenance, such as checking for wear and tear, cleaning, and lubricating as needed. Follow the manufacturer's recommended maintenance schedule for best results. 5.How does a gear motor compare to other types of motors? We focus on innovation and continuous improvement to maintain a competitive advantage. A gear motor is a type of motor that combines a motor and a gearbox into one unit. This allows for increased torque and reduced speed, making it suitable for applications that require high torque and low speed, such as in industrial machinery, robotics, and automotive systems.
Compared to other types of motors, such as DC motors, AC motors, and stepper motors, gear motors have the following advantages:
1. High torque: Gear motors have a higher torque output compared to other types of motors, making them suitable for heavy-duty applications.
2. Precise speed control: The gearbox in a gear motor allows for precise speed control, making it ideal for applications that require a specific speed.
3. Compact size: Gear motors are compact in size, making them suitable for applications where space is limited.
4. Low maintenance: The gearbox in a gear motor helps to reduce wear and tear on the motor, resulting in lower maintenance requirements.
5. Cost-effective: Gear motors are generally more cost-effective compared to other types of motors, making them a popular choice for many applications.
6.What are the operating temperature ranges for gear motors? We have a wide range of coreless motor sizes customer groups and establishes long -term cooperative relationships with partners. The countries we provide services include Ukraine,Juan de Nova Island,Kazakhstan,Tokelau,Timor-Leste,Tuvalu. The operating temperature ranges for gear motors can vary depending on the specific type and model. However, in general, most gear motors have an operating temperature range of -10°C to 40°C (14°F to 104°F). Some gear motors may have a wider range, up to -40°C to 70°C (-40°F to 158°F), while others may have a narrower range, such as 0°C to 30°C (32°F to 86°F). It is important to check the specifications of the specific gear motor to determine its operating temperature range. 7.What are the differences between helical, spur, and planetary gear motors? We are committed to providing personalized solutions and established long -term strategic cooperative relationships with customers.
Helical, spur, and planetary gear motors are all types of gear motors used for power transmission and motion control. They differ in their design, construction, and application.
1. Helical Gear Motors: - Helical gear motors have helical gears that are cut at an angle to the axis of rotation. - The teeth of the gears are curved, which allows for smoother and quieter operation compared to other types of gear motors. - They have a higher load-carrying capacity and can transmit more torque than spur gear motors. - Helical gear motors are commonly used in heavy-duty applications such as industrial machinery, construction equipment, and vehicles.
2. Spur Gear Motors:
- Spur gear motors have straight-cut gears that are mounted on parallel shafts. - The teeth of the gears are straight and mesh directly with each other, resulting in a simple and efficient design. - They are compact, lightweight, and cost-effective, making them suitable for a wide range of applications. - However, they are not as efficient as helical gear motors and produce more noise and vibration.
3. Planetary Gear Motors: - Planetary gear motors have a central gear (sun gear) that meshes with multiple smaller gears (planet gears) arranged around it. - The planet gears rotate on their own axes and also revolve around the sun gear, resulting in a compact and efficient design. - They have a high gear ratio and can transmit a large amount of torque in a small package. - Planetary gear motors are commonly used in precision applications such as robotics, medical equipment, and aerospace.
In summary, the main differences between helical, spur, and planetary gear motors are their gear design, load-carrying capacity, efficiency, and application. Helical gear motors are best suited for heavy-duty applications, spur gear motors are suitable for general-purpose use, and planetary gear motors are ideal for precision applications. 8.What are the advantages of a gear motor? We have a good reputation and image in the industry. The quality and price advantage of coreless motor sizes products is an important factor in our hard overseas market. 1. High torque: Gear motors are designed to provide high torque output, making them suitable for heavy-duty applications.
2. Compact size: Gear motors are compact in size, which makes them ideal for use in tight spaces where a larger motor may not fit.
3. Efficiency: Gear motors are highly efficient, with most models having an efficiency rate of over 90%. This means that they can convert a high percentage of electrical energy into mechanical energy.
4. Versatility: Gear motors can be used in a wide range of applications, including industrial machinery, automotive systems, and household appliances.
5. Speed control: Gear motors can be easily controlled to achieve different speeds, making them suitable for applications that require precise speed control.
6. Durability: Gear motors are designed to be durable and long-lasting, with most models having a lifespan of over 10,000 hours.
7. Low maintenance: Due to their simple design and fewer moving parts, gear motors require less maintenance compared to other types of motors.
8. Cost-effective: Gear motors are relatively inexpensive compared to other types of motors, making them a cost-effective option for many applications.
9. Quiet operation: Gear motors operate quietly, making them suitable for use in noise-sensitive environments.
10. Easy installation: Gear motors are easy to install and can be mounted in various orientations, making them suitable for a wide range of applications. 9.What controls are necessary for operating a gear motor? Our coreless motor sizes products undergo strict quality control to ensure customer satisfaction.
1. Power source: A gear motor requires a power source, such as an electrical outlet or battery, to operate. 2. On/off switch: A simple on/off switch is necessary to start and stop the gear motor.
3. Speed control: Some gear motors may have a speed control feature, allowing the user to adjust the speed of the motor according to their needs.
4. Direction control: Depending on the application, a gear motor may need to rotate in both clockwise and counterclockwise directions. In such cases, a direction control switch is necessary.
5. Overload protection: To prevent damage to the motor, an overload protection mechanism, such as a fuse or circuit breaker, should be in place.
6. Enclosure: A gear motor should be enclosed in a protective casing to prevent any accidents or damage to the motor.
7. Mounting options: Depending on the application, a gear motor may need to be mounted in a specific position. Therefore, it is essential to have suitable mounting options, such as brackets or flanges, for the motor.
8. Lubrication: Gear motors require regular lubrication to ensure smooth operation and prevent wear and tear. A lubrication system or access point should be included in the design.
9. Temperature control: Some gear motors may generate a significant amount of heat during operation. To prevent overheating, a temperature control mechanism, such as a cooling fan, may be necessary.
10. Maintenance and troubleshooting instructions: Proper maintenance and troubleshooting instructions should be provided with the gear motor to ensure its longevity and safe operation. 10.What are the differences between AC and DC gear motors? We maintain a certain amount of R&D investment every year and continuously improve operational efficiency to provide better services to our cooperative customers. 1. Power Source: The main difference between AC and DC gear motors is their power source. AC gear motors are powered by alternating current, while DC gear motors are powered by direct current.
2. Voltage: AC gear motors typically operate at higher voltages (usually 110-240V), while DC gear motors operate at lower voltages (usually 12-24V).
3. Speed Control: AC gear motors have a fixed speed, which is determined by the frequency of the AC power supply. On the other hand, DC gear motors have variable speed control, allowing for more precise speed adjustments.
4. Direction of Rotation: AC gear motors can rotate in both clockwise and counterclockwise directions, while DC gear motors can only rotate in one direction unless a reversing switch is added.
5. Efficiency: DC gear motors are generally more efficient than AC gear motors, as they do not require a transformer to convert the power source.
6. Size and Weight: AC gear motors are typically larger and heavier than DC gear motors, as they require additional components such as a transformer and capacitor.
7. Cost: AC gear motors are generally more expensive than DC gear motors due to their more complex design and higher voltage requirements.
8. Maintenance: DC gear motors require less maintenance compared to AC gear motors, as they have fewer moving parts and do not require a transformer.
|