Mercury Motion is a Chinese manufacturer of DC motors and DC gear motors. With years of experiences on designing and manufacturing, we are capable of making DC motors with custom specifications and providing comprehensive solutions to our customers' applications.Our motors are applied on a wide range of automatic and intelligent products, including but not limited to health equipment and etc.
We have professional R&D, QC and sales team. we also have adequate production facilities and advanced testing equipment. We always focus on improving our products and the quality control system.We always keep a close watch to the market and try to provide you the best of our service. Most of our customers are from Comoros,Turkmenistan,Iceland,Malawi,Croatia,Greenland,Faroe Islands and domestic market.
Product name
| coreless motor size 408
| Keyword
| coreless motor esc,coreless motor sizes,coreless motor speed controller,coreless motor gears,coreless motor speed control,coreless motor drone
| Place of Origin | China | Rated
| DC 5V
| Type
| GEAR MOTOR
| Total length
| 74.6-51.1mm, (Contact us for specific information to confirm)
| Applicable Industries
| advanced toys, etc.
| Weight
| 11kg
| Product Description
| A gear motor is a type of motor that incorporates gears into its design to achieve a specific speed and torque output. It typically consists of a motor, a gearbox, and a series of gears that work together to control the motor's speed and power.
| Life span
| 13 years (Contact us for specific information to confirm)
| Advantage
| We keep good quality and competitive price to ensure our customers benefit
| Packing
| 136x81x70mm(Contact us for specific information to confirm)
| Sales country
| All over the world for example:Comoros,Turkmenistan,Iceland,Malawi,Croatia,Greenland,Faroe Islands
| MOQ
| 25pcs(Contact us for specific information to confirm)
|
Please contact us for details about Precision Motors
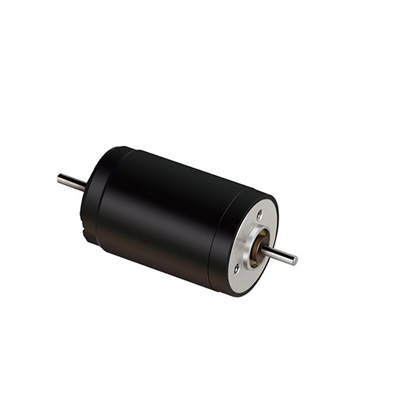
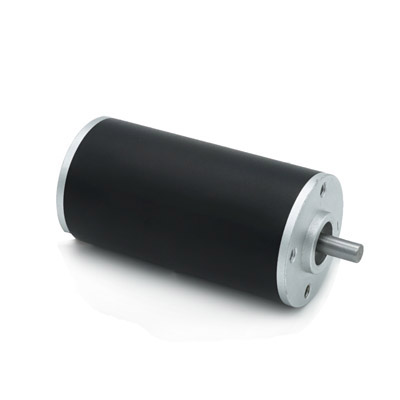
For more information about GM Planetary Gear Motors, please contact us. 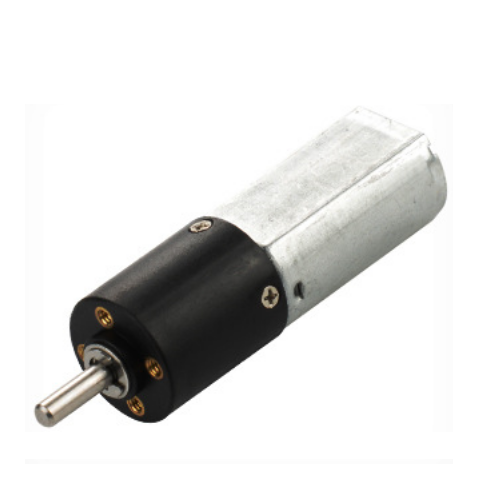
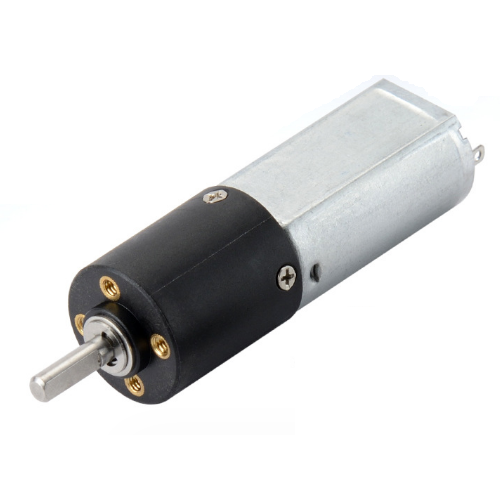
Please contact us for details about Spur Gear Motors 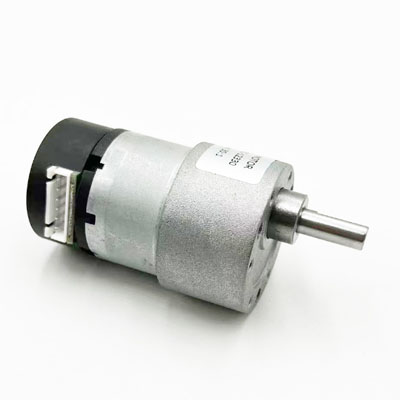
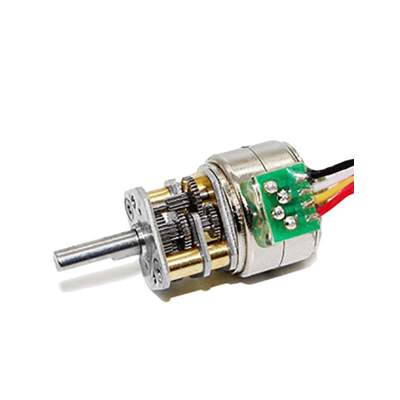
coreless motor size 408 services FAQs Guide
Are you looking for a quick review guide about coreless motor size 408services?
An ultimate FAQ buying guide is available to help you.This guide contains all the information about all the important facts, figures, and various processes regarding coreless motor size 408 services.
Let’s continue!
1.How does lubrication affect the performance of a gear motor? 2.How does the gear design affect the performance of a gear motor? 3.Can gear motors be reversible? 4.What are the differences between AC and DC gear motors? 5.How do you troubleshoot common issues with gear motors? 6.What are the different types of gear motors available? 7.How does the speed of a gear motor affect its torque? 8.Can gear motors handle varying load demands? 9.How do you calculate the gear ratio for a gear motor? 10.Can gear motors be used in harsh environments? 1.How does lubrication affect the performance of a gear motor? Our mission is to provide customers with the best solutions for coreless motor size 408. Lubrication plays a crucial role in the performance of a gear motor. It helps to reduce friction between the moving parts of the motor, which in turn reduces wear and tear and increases the lifespan of the motor. Here are some ways in which lubrication affects the performance of a gear motor:
1. Reduces friction: The primary function of lubrication is to reduce friction between the moving parts of the gear motor. Friction can cause heat build-up, which can lead to premature wear and tear of the motor. By reducing friction, lubrication helps to improve the efficiency of the motor and reduce energy consumption.
2. Prevents wear and tear: The gears in a gear motor are constantly in contact with each other, which can cause wear and tear over time. Lubrication forms a protective layer between the gears, preventing direct metal-to-metal contact and reducing the rate of wear and tear.
3. Improves efficiency: A well-lubricated gear motor operates more smoothly and efficiently. This is because lubrication reduces the resistance between the gears, allowing them to move more freely and with less effort. This, in turn, leads to improved performance and energy efficiency.
4. Reduces noise and vibration: Friction between the gears can also cause noise and vibration, which can be disruptive and damaging to the motor. Lubrication helps to dampen these effects, resulting in a quieter and smoother operation of the gear motor.
5. Protects against corrosion: Lubrication also helps to protect the gears and other components of the motor from corrosion. This is especially important in harsh environments where the motor is exposed to moisture or other corrosive substances.
In summary, proper lubrication is essential for the smooth and efficient operation of a gear motor. It helps to reduce friction, prevent wear and tear, improve efficiency, reduce noise and vibration, and protect against corrosion. Regular maintenance and proper lubrication can significantly extend the lifespan of a gear motor and ensure optimal performance. 2.How does the gear design affect the performance of a gear motor? We have a first -class management team, and we pay attention to teamwork to achieve common goals. The gear design plays a crucial role in determining the performance of a gear motor. Some of the ways in which the gear design affects the performance are:
1. Speed and Torque: The gear design determines the speed and torque output of the gear motor. A gear motor with a higher gear ratio will have a lower speed but higher torque output, while a gear motor with a lower gear ratio will have a higher speed but lower torque output.
2. Efficiency: The gear design also affects the efficiency of the gear motor. A well-designed gear system can minimize friction and maximize power transfer, resulting in higher efficiency.
3. Noise and Vibration: The gear design can also impact the noise and vibration levels of the gear motor. A poorly designed gear system can produce excessive noise and vibration, leading to reduced performance and increased wear and tear.
4. Load Capacity: The gear design also determines the load capacity of the gear motor. A gear motor with a robust and well-designed gear system can handle heavier loads without compromising its performance.
5. Durability: The gear design can also affect the durability of the gear motor. A well-designed gear system can withstand high levels of stress and wear, resulting in a longer lifespan for the gear motor.
Overall, the gear design is a critical factor in determining the performance, efficiency, and durability of a gear motor. A well-designed gear system can significantly improve the overall performance of the gear motor, while a poorly designed one can lead to various issues and reduce its effectiveness. 3.Can gear motors be reversible? We pay attention to employee development and benefits, and provide a good working environment in order to improve the efficiency of employees and improve the quality management of coreless motor size 408 products. Yes, gear motors can be reversible. Reversible gear motors have the ability to rotate in both clockwise and counterclockwise directions, allowing for bidirectional movement. This is achieved by using a reversible motor and a gear train with two sets of gears that can be engaged or disengaged to change the direction of rotation. Reversible gear motors are commonly used in applications such as robotics, conveyor systems, and garage door openers. 4.What are the differences between AC and DC gear motors? We maintain a certain amount of R&D investment every year and continuously improve operational efficiency to provide better services to our cooperative customers. 1. Power Source: The main difference between AC and DC gear motors is their power source. AC gear motors are powered by alternating current, while DC gear motors are powered by direct current.
2. Voltage: AC gear motors typically operate at higher voltages (usually 110-240V), while DC gear motors operate at lower voltages (usually 12-24V).
3. Speed Control: AC gear motors have a fixed speed, which is determined by the frequency of the AC power supply. On the other hand, DC gear motors have variable speed control, allowing for more precise speed adjustments.
4. Direction of Rotation: AC gear motors can rotate in both clockwise and counterclockwise directions, while DC gear motors can only rotate in one direction unless a reversing switch is added.
5. Efficiency: DC gear motors are generally more efficient than AC gear motors, as they do not require a transformer to convert the power source.
6. Size and Weight: AC gear motors are typically larger and heavier than DC gear motors, as they require additional components such as a transformer and capacitor.
7. Cost: AC gear motors are generally more expensive than DC gear motors due to their more complex design and higher voltage requirements.
8. Maintenance: DC gear motors require less maintenance compared to AC gear motors, as they have fewer moving parts and do not require a transformer.
5.How do you troubleshoot common issues with gear motors? We continue to improve coreless motor size 408 products and processes to improve efficiency. 1. Check the power supply: Make sure the gear motor is receiving the correct voltage and that the power supply is functioning properly.
2. Inspect the wiring: Check for loose or damaged wires, and make sure they are connected to the correct terminals.
3. Check for mechanical obstructions: Make sure there are no obstructions preventing the gear motor from turning, such as debris or misaligned gears.
4. Lubricate the gears: If the gear motor is making unusual noises or is not turning smoothly, it may need to be lubricated. Use a suitable lubricant according to the manufacturer's recommendations.
5. Check for overheating: If the gear motor feels hot to the touch, it may be overheating. This could be due to a faulty motor or excessive load on the motor. Reduce the load or replace the motor if necessary.
6. Test the motor with a multimeter: Use a multimeter to check the voltage and current of the gear motor. This can help identify any electrical issues.
7. Inspect the motor brushes: If the gear motor has carbon brushes, check them for wear and replace if necessary.
8. Check the motor bearings: If the gear motor has bearings, check them for wear and replace if necessary.
9. Consult the manufacturer's manual: If the gear motor is still not functioning properly, refer to the manufacturer's manual for troubleshooting tips specific to your model.
10. Seek professional help: If you are unable to identify or fix the issue, it may be best to seek help from a professional technician or contact the manufacturer for assistance. 6.What are the different types of gear motors available? Being one of the top coreless motor size 408 manufacturers in China, We attach great importance to this detail. 1. DC Gear Motors: These motors use direct current (DC) power supply and are commonly used in applications that require precise speed control and high torque.
2. AC Gear Motors: These motors use alternating current (AC) power supply and are commonly used in industrial and commercial applications.
3. Stepper Gear Motors: These motors use a series of electromagnetic coils to rotate the motor shaft in small, precise steps. They are commonly used in robotics and automation applications.
4. Servo Gear Motors: These motors use a closed-loop control system to accurately control the speed and position of the motor shaft. They are commonly used in industrial and robotic applications.
5. Worm Gear Motors: These motors use a worm gear mechanism to reduce the speed of the motor and increase the torque output. They are commonly used in heavy-duty applications.
6. Planetary Gear Motors: These motors use a planetary gear system to achieve high torque and precise speed control. They are commonly used in robotics, automation, and automotive applications.
7. Helical Gear Motors: These motors use helical gears to achieve high efficiency and smooth operation. They are commonly used in industrial and commercial applications.
8. Bevel Gear Motors: These motors use bevel gears to transfer power between two intersecting shafts. They are commonly used in applications that require a change in direction of the motor shaft.
9. Spur Gear Motors: These motors use spur gears to transfer power between parallel shafts. They are commonly used in low-speed, high-torque applications.
10. Rack and Pinion Gear Motors: These motors use a rack and pinion mechanism to convert rotational motion into linear motion. They are commonly used in applications such as elevators and CNC machines. 7.How does the speed of a gear motor affect its torque? We should perform well in market competition, and the prices of coreless motor size 408 products have a great competitive advantage. The speed of a gear motor does not directly affect its torque. Torque is a measure of the rotational force produced by the motor, while speed is a measure of how fast the motor can rotate. However, the gear ratio of the motor can indirectly affect its torque. A higher gear ratio means that the motor will have more torque but a lower speed, while a lower gear ratio means that the motor will have less torque but a higher speed. This is because the gear ratio determines the mechanical advantage of the motor, which is the ratio of the output torque to the input torque. Therefore, the speed of a gear motor can be adjusted by changing the gear ratio, which will in turn affect its torque. 8.Can gear motors handle varying load demands? We have been working hard to improve service quality and meet customer needs. Yes, gear motors are designed to handle varying load demands. The gear ratio of the motor allows it to provide the necessary torque to handle different load demands. Additionally, some gear motors have adjustable speed and torque settings, making them even more versatile in handling varying load demands. 9.How do you calculate the gear ratio for a gear motor? Our products & services cover a wide range of areas and meet the needs of different fields. The gear ratio for a gear motor can be calculated by dividing the number of teeth on the driven gear (the gear attached to the output shaft) by the number of teeth on the driving gear (the gear attached to the motor shaft). This can be expressed as a ratio, such as 2:1 or 3:1, or as a decimal, such as 0.5 or 0.33.
For example, if the driven gear has 20 teeth and the driving gear has 10 teeth, the gear ratio would be 20/10 = 2:1 or 20 ÷ 10 = 2. This means that for every one revolution of the motor shaft, the output shaft will make two revolutions.
It is important to note that the gear ratio only takes into account the number of teeth on the gears and does not consider the size or diameter of the gears. The size of the gears can also affect the overall speed and torque of the gear motor. 10.Can gear motors be used in harsh environments? We have flexible production capacity. Whether you are large orders or small orders, you can produce and release goods in a timely manner to meet customer needs. Yes, gear motors can be used in harsh environments, but it is important to choose the right type of gear motor for the specific environment. For example, gear motors with sealed housings and corrosion-resistant materials are better suited for outdoor or wet environments, while gear motors with high temperature ratings are better for use in hot environments. It is also important to regularly maintain and lubricate gear motors used in harsh environments to ensure their longevity and performance.
|