Mercury Motion is specializing in specializes in high end micro motors, gear motors and their respective parts since 2009. Our products are widely used in entertainment systems, automobiles, home and industrial appliances and many others with good reputations. We have good qualified R&D enginneers to make all motor meet customer required . We do big quantity orders as well as small orders.
Product name
| coreless motor inside
| Keyword
| coreless motor speed control,coreless motor inside,coreless motor speed controller,coreless motor gears,coreless motor drone,coreless motor gearbox,coreless motor esc,coreless motor sizes
| Place of Origin | China | Rated
| DC 5V
| Type
| GEAR MOTOR
| Total length
| 73.8-56.3mm, (Contact us for specific information to confirm)
| Applicable Industries
| electrical devices, etc.
| Weight
| 15kg
| Product Description
| A gear motor is a type of motor that incorporates gears into its design to achieve a specific speed and torque output. It typically consists of a motor, a gearbox, and a series of gears that work together to control the motor's speed and power.
| Life span
| 20 years (Contact us for specific information to confirm)
| Advantage
| We keep good quality and competitive price to ensure our customers benefit
| Packing
| 110x144x111mm(Contact us for specific information to confirm)
| Sales country
| All over the world for example:Burkina Faso,Israel,Turks and Caicos Islands,Grenada,Zimbabwe,Barbados,Guyana,Christmas Island
| Certification
| ISO9001
| color
| black/grey
| MOQ
| 41pcs(Contact us for specific information to confirm)
|
Please contact us for details about Precision Motors
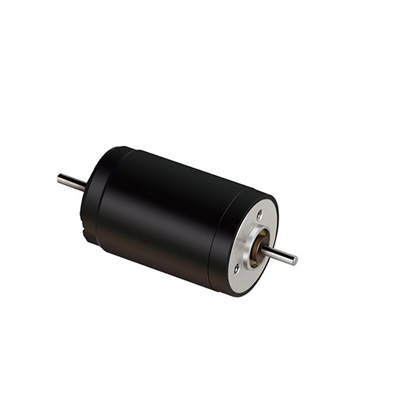
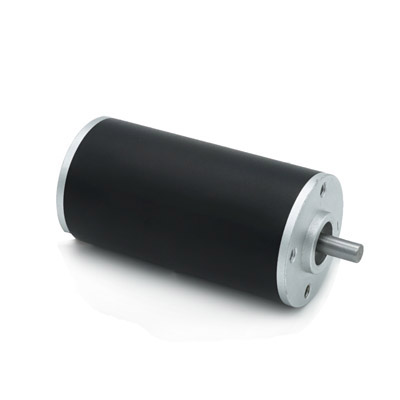
For more information about GM Planetary Gear Motors, please contact us. 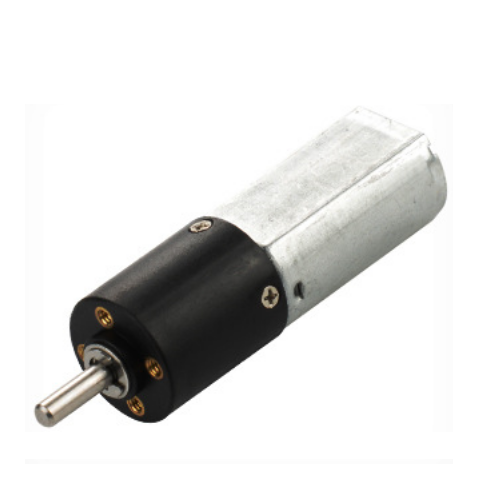
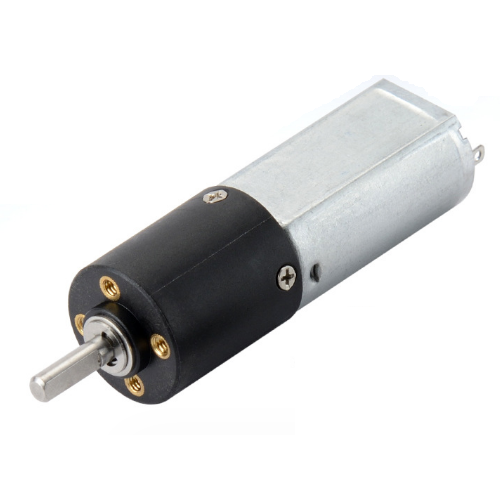
Please contact us for details about Spur Gear Motors 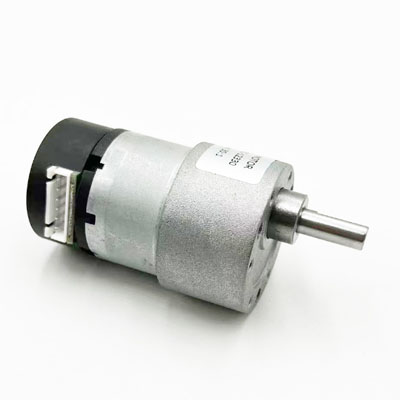
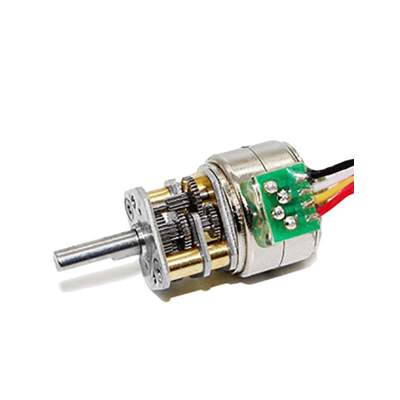
coreless motor inside services FAQs Guide
Are you looking for a quick review guide about coreless motor insideservices?
An ultimate FAQ buying guide is available to help you.This guide contains all the information about all the important facts, figures, and various processes regarding coreless motor inside services.
Let’s continue!
1.What are the operating temperature ranges for gear motors? 2.How does the gear design affect the performance of a gear motor? 3.Can gear motors handle varying load demands? 4.How does the gear ratio affect the performance of a gear motor? 5.Are there any noise or vibration concerns with gear motors? 6.How does the size of a gear motor affect its performance? 7.How does lubrication affect the performance of a gear motor? 8.What types of bearings are typically used in gear motors? 9.How durable are gear motors and what is their expected lifespan? 10.What are the different types of gear motors available? 1.What are the operating temperature ranges for gear motors? We have a wide range of coreless motor inside customer groups and establishes long -term cooperative relationships with partners. The countries we provide services include Burkina Faso,Israel,Turks and Caicos Islands,Grenada,Zimbabwe,Barbados,Guyana,Christmas Island. The operating temperature ranges for gear motors can vary depending on the specific type and model. However, in general, most gear motors have an operating temperature range of -10°C to 40°C (14°F to 104°F). Some gear motors may have a wider range, up to -40°C to 70°C (-40°F to 158°F), while others may have a narrower range, such as 0°C to 30°C (32°F to 86°F). It is important to check the specifications of the specific gear motor to determine its operating temperature range. 2.How does the gear design affect the performance of a gear motor? We have a first -class management team, and we pay attention to teamwork to achieve common goals. The gear design plays a crucial role in determining the performance of a gear motor. Some of the ways in which the gear design affects the performance are:
1. Speed and Torque: The gear design determines the speed and torque output of the gear motor. A gear motor with a higher gear ratio will have a lower speed but higher torque output, while a gear motor with a lower gear ratio will have a higher speed but lower torque output.
2. Efficiency: The gear design also affects the efficiency of the gear motor. A well-designed gear system can minimize friction and maximize power transfer, resulting in higher efficiency.
3. Noise and Vibration: The gear design can also impact the noise and vibration levels of the gear motor. A poorly designed gear system can produce excessive noise and vibration, leading to reduced performance and increased wear and tear.
4. Load Capacity: The gear design also determines the load capacity of the gear motor. A gear motor with a robust and well-designed gear system can handle heavier loads without compromising its performance.
5. Durability: The gear design can also affect the durability of the gear motor. A well-designed gear system can withstand high levels of stress and wear, resulting in a longer lifespan for the gear motor.
Overall, the gear design is a critical factor in determining the performance, efficiency, and durability of a gear motor. A well-designed gear system can significantly improve the overall performance of the gear motor, while a poorly designed one can lead to various issues and reduce its effectiveness. 3.Can gear motors handle varying load demands? We have been working hard to improve service quality and meet customer needs. Yes, gear motors are designed to handle varying load demands. The gear ratio of the motor allows it to provide the necessary torque to handle different load demands. Additionally, some gear motors have adjustable speed and torque settings, making them even more versatile in handling varying load demands. 4.How does the gear ratio affect the performance of a gear motor? We pay attention to the transformation of intellectual property protection and innovation achievements. Your OEM or ODM order design we have a complete confidentiality system. The gear ratio of a gear motor refers to the ratio of the number of teeth on the input gear to the number of teeth on the output gear. This ratio has a significant impact on the performance of the gear motor in terms of speed, torque, and efficiency.
1. Speed: The gear ratio determines the speed at which the output shaft of the gear motor rotates in relation to the input shaft. A higher gear ratio means that the output shaft will rotate at a slower speed compared to the input shaft. This is because the output gear has fewer teeth than the input gear, resulting in a lower rotational speed. On the other hand, a lower gear ratio will result in a higher output speed.
2. Torque: The gear ratio also affects the torque output of the gear motor. Torque is the rotational force produced by the motor, and it is directly proportional to the gear ratio. A higher gear ratio will result in a higher torque output, while a lower gear ratio will result in a lower torque output. This is because a higher gear ratio allows the motor to multiply the torque from the input shaft to the output shaft.
3. Efficiency: The gear ratio also plays a role in the efficiency of the gear motor. In general, a higher gear ratio will result in a lower efficiency, while a lower gear ratio will result in a higher efficiency. This is because a higher gear ratio requires more gear teeth to mesh, resulting in more friction and energy loss. On the other hand, a lower gear ratio requires fewer gear teeth to mesh, resulting in less friction and higher efficiency.
In summary, the gear ratio of a gear motor has a significant impact on its performance, with higher gear ratios resulting in slower speed, higher torque, and lower efficiency, and lower gear ratios resulting in higher speed, lower torque, and higher efficiency. The appropriate gear ratio for a gear motor will depend on the specific application and the desired performance requirements.
5.Are there any noise or vibration concerns with gear motors? We have broad development space in domestic and foreign markets. coreless motor inside have great advantages in terms of price, quality, and delivery date. There can be noise and vibration concerns with gear motors, depending on the type and quality of the motor. Some gear motors may produce a humming or buzzing noise, while others may have a more noticeable vibration. This can be caused by factors such as the type of gears used, the speed and load of the motor, and the overall design and construction of the motor. In general, higher quality gear motors will have better noise and vibration control measures in place to minimize these concerns. It is important to carefully consider the specifications and reviews of a gear motor before purchasing to ensure it meets your noise and vibration requirements. 6.How does the size of a gear motor affect its performance? We focus on providing high coreless motor inside quality products and services.
The size of a gear motor can affect its performance in several ways:
1. Torque: The size of the gear motor directly affects the amount of torque it can produce. A larger gear motor will have a larger gear ratio, which means it can produce more torque. This is important for applications that require high torque, such as lifting heavy loads.
2. Speed: The size of the gear motor also affects its speed. A larger gear motor will have a slower speed due to the larger gear ratio. This is important for applications that require precise and slow movements, such as in robotics.
3. Power: The size of the gear motor also affects its power output. A larger gear motor will have a higher power output due to the larger gear ratio and larger motor size. This is important for applications that require high power, such as in industrial machinery.
4. Efficiency: The size of the gear motor can also affect its efficiency. A larger gear motor may have a higher efficiency due to the larger gear ratio, which reduces the amount of energy lost in the gear train. However, this also depends on the quality and design of the gear motor.
5. Durability: The size of the gear motor can also affect its durability. A larger gear motor may be more durable due to the larger size and stronger components. This is important for applications that require frequent and heavy use.
Overall, the size of a gear motor plays a crucial role in its performance and should be carefully considered when selecting a motor for a specific application. 7.How does lubrication affect the performance of a gear motor? Our mission is to provide customers with the best solutions for coreless motor inside. Lubrication plays a crucial role in the performance of a gear motor. It helps to reduce friction between the moving parts of the motor, which in turn reduces wear and tear and increases the lifespan of the motor. Here are some ways in which lubrication affects the performance of a gear motor:
1. Reduces friction: The primary function of lubrication is to reduce friction between the moving parts of the gear motor. Friction can cause heat build-up, which can lead to premature wear and tear of the motor. By reducing friction, lubrication helps to improve the efficiency of the motor and reduce energy consumption.
2. Prevents wear and tear: The gears in a gear motor are constantly in contact with each other, which can cause wear and tear over time. Lubrication forms a protective layer between the gears, preventing direct metal-to-metal contact and reducing the rate of wear and tear.
3. Improves efficiency: A well-lubricated gear motor operates more smoothly and efficiently. This is because lubrication reduces the resistance between the gears, allowing them to move more freely and with less effort. This, in turn, leads to improved performance and energy efficiency.
4. Reduces noise and vibration: Friction between the gears can also cause noise and vibration, which can be disruptive and damaging to the motor. Lubrication helps to dampen these effects, resulting in a quieter and smoother operation of the gear motor.
5. Protects against corrosion: Lubrication also helps to protect the gears and other components of the motor from corrosion. This is especially important in harsh environments where the motor is exposed to moisture or other corrosive substances.
In summary, proper lubrication is essential for the smooth and efficient operation of a gear motor. It helps to reduce friction, prevent wear and tear, improve efficiency, reduce noise and vibration, and protect against corrosion. Regular maintenance and proper lubrication can significantly extend the lifespan of a gear motor and ensure optimal performance. 8.What types of bearings are typically used in gear motors? We adhere to the principle of integrity and transparency, and establish long -term relationships with partners, and we attach great importance to this detail. 1. Ball bearings: These are the most common type of bearings used in gear motors. They consist of a series of balls held in place by a cage, which allows for smooth rotation and reduced friction.
2. Roller bearings: These bearings use cylindrical rollers instead of balls to reduce friction and support heavy loads. They are commonly used in high-speed gear motors.
3. Tapered roller bearings: These bearings have tapered rollers that are designed to handle both radial and axial loads. They are commonly used in gear motors that require high precision and durability.
4. Needle bearings: These bearings use long, thin rollers to support heavy loads and reduce friction. They are commonly used in gear motors with limited space.
5. Thrust bearings: These bearings are designed to handle axial loads and are commonly used in gear motors that require high thrust capacity.
6. Spherical roller bearings: These bearings have a spherical outer raceway, which allows for misalignment and can handle heavy radial loads. They are commonly used in gear motors that operate at high speeds.
7. Cylindrical roller bearings: These bearings use cylindrical rollers to support heavy radial loads and are commonly used in gear motors with high radial load requirements.
8. Bushings: These are simple bearings that consist of a smooth cylindrical or spherical surface that allows for rotation with minimal friction. They are commonly used in low-speed gear motors.
9. Plain bearings: These bearings have a smooth surface that allows for sliding motion and are commonly used in gear motors that require low friction and high precision.
10. Magnetic bearings: These bearings use magnetic fields to support the rotating shaft and eliminate the need for physical contact. They are commonly used in high-speed gear motors that require low friction and high precision. 9.How durable are gear motors and what is their expected lifespan? We have a professional team that is committed to the innovation and development of coreless motor inside. The durability of gear motors can vary depending on the quality of the motor and the conditions in which it is used. Generally, gear motors are designed to be durable and have a long lifespan. They are often used in industrial and commercial applications where they are subjected to heavy use and harsh environments.
The expected lifespan of a gear motor can range from 5 to 20 years, depending on the type of motor and its usage. Factors that can affect the lifespan of a gear motor include the quality of the materials used, the maintenance and care of the motor, and the load and speed at which it is operated.
Some gear motors may also come with a warranty that guarantees a certain lifespan. It is important to follow the manufacturer's recommendations for maintenance and usage to ensure the longest possible lifespan for your gear motor. 10.What are the different types of gear motors available? Being one of the top coreless motor inside manufacturers in China, We attach great importance to this detail. 1. DC Gear Motors: These motors use direct current (DC) power supply and are commonly used in applications that require precise speed control and high torque.
2. AC Gear Motors: These motors use alternating current (AC) power supply and are commonly used in industrial and commercial applications.
3. Stepper Gear Motors: These motors use a series of electromagnetic coils to rotate the motor shaft in small, precise steps. They are commonly used in robotics and automation applications.
4. Servo Gear Motors: These motors use a closed-loop control system to accurately control the speed and position of the motor shaft. They are commonly used in industrial and robotic applications.
5. Worm Gear Motors: These motors use a worm gear mechanism to reduce the speed of the motor and increase the torque output. They are commonly used in heavy-duty applications.
6. Planetary Gear Motors: These motors use a planetary gear system to achieve high torque and precise speed control. They are commonly used in robotics, automation, and automotive applications.
7. Helical Gear Motors: These motors use helical gears to achieve high efficiency and smooth operation. They are commonly used in industrial and commercial applications.
8. Bevel Gear Motors: These motors use bevel gears to transfer power between two intersecting shafts. They are commonly used in applications that require a change in direction of the motor shaft.
9. Spur Gear Motors: These motors use spur gears to transfer power between parallel shafts. They are commonly used in low-speed, high-torque applications.
10. Rack and Pinion Gear Motors: These motors use a rack and pinion mechanism to convert rotational motion into linear motion. They are commonly used in applications such as elevators and CNC machines.
|