Founded in 2009,Mercury Motion specializes in high end micro motors, such as brushless motors, gear motors, stepper motors…etc.Especially the precision gear motors, we could design and produce all the gears and we have a full production line of CNC center .This combination makes us have the unique advantage of the gear motors industry. Our motors are widely used in cars, home appliances,medical equipment, electrical devices, ATMs and robots, etc.
Let’s continue! 1.Is a gear motor suitable for continuous operation? 2.What are the common noise levels of gear motors? 3.How to improve the efficiency of a gear motor? 4.Can gear motors be submerged in water? 5.How to choose the right voltage for a gear motor? 6.What are the accessories and add-ons available for gear motors? 1.Is a gear motor suitable for continuous operation? Yes, a gear motor is suitable for continuous operation. Gear motors are designed to provide consistent and reliable power output over extended periods of time. They are commonly used in industrial and commercial applications where continuous operation is required, such as in conveyor systems, pumps, and machinery. However, the specific type and size of gear motor needed for continuous operation will depend on the specific application and load requirements. It is important to consult with a professional to ensure the gear motor is properly sized and rated for the intended use. 2.What are the common noise levels of gear motors? The common noise levels of gear motors can vary depending on the type and size of the motor, as well as the speed and load it is operating at. However, on average, gear motors can produce noise levels ranging from 50-80 decibels (dB) at a distance of 1 meter. This is equivalent to the noise level of a normal conversation or a vacuum cleaner. Some larger or high-speed gear motors may produce noise levels up to 90 dB or higher. 3.How to improve the efficiency of a gear motor? 1. Use high-quality gears: The quality of the gears used in a gear motor greatly affects its efficiency. High-quality gears with precise teeth and smooth surfaces can reduce friction and improve the overall efficiency of the motor.
2. Lubrication: Proper lubrication is essential for reducing friction and wear in the gears. This can significantly improve the efficiency of the gear motor. Make sure to use the recommended lubricant and regularly check and replace it as needed.
3. Reduce load: The load on the gear motor can greatly affect its efficiency. If possible, try to reduce the load on the motor by using a larger gear or reducing the load on the machine it is powering.
4. Proper alignment: Misalignment of gears can cause increased friction and reduce the efficiency of the gear motor. Make sure to properly align the gears during installation and regularly check for any misalignment.
5. Use the right motor size: Using a motor that is too small for the required load can cause it to work harder and reduce its efficiency. Make sure to choose the right motor size for the specific application to ensure optimal efficiency.
6. Regular maintenance: Regular maintenance and inspection of the gear motor can help identify any issues that may be affecting its efficiency. This can include checking for wear and tear, lubrication levels, and proper alignment.
7. Use a variable speed drive: A variable speed drive can help optimize the speed of the gear motor based on the load, reducing energy consumption and improving efficiency.
8. Reduce friction: Friction is the biggest enemy of efficiency in a gear motor. Minimizing friction can be achieved by using high-quality gears, proper lubrication, and regular maintenance.
9. Upgrade to a more efficient motor: If the gear motor is old or outdated, consider upgrading to a more efficient motor. Newer models often have improved designs and technologies that can significantly improve efficiency.
10. Consider alternative power sources: In some cases, using alternative power sources such as electric motors or hydraulic motors can be more efficient than traditional gear motors. Consider the specific application and choose the most efficient power source for the job. 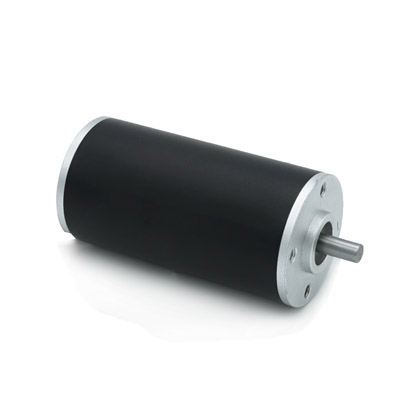
4.Can gear motors be submerged in water? It depends on the specific gear motor and its IP (Ingress Protection) rating. Some gear motors are designed to be waterproof and can be submerged in water, while others are not and should not be exposed to water. It is important to check the manufacturer's specifications and IP rating before submerging a gear motor in water. 5.How to choose the right voltage for a gear motor? 1. Determine the motor's rated voltage: The first step in choosing the right voltage for a gear motor is to determine the motor's rated voltage. This information can usually be found on the motor's label or in the manufacturer's specifications.
2. Consider the power supply: The voltage of the power supply that will be used to operate the gear motor is an important factor to consider. The motor's rated voltage should match the voltage of the power supply to ensure proper operation.
3. Check the gear ratio: The gear ratio of a gear motor is the ratio of the number of teeth on the input gear to the number of teeth on the output gear. A higher gear ratio means the motor will have more torque but will require a higher voltage to operate.
4. Consider the load: The load that the gear motor will be driving is also an important factor to consider when choosing the right voltage. If the load is heavy or requires a lot of torque, a higher voltage may be necessary to ensure the motor can handle the load.
5. Consult the manufacturer's recommendations: The manufacturer of the gear motor may have specific recommendations for the voltage that should be used. It is always a good idea to consult the manufacturer's specifications or contact them directly for guidance.
6. Consider the application: The application in which the gear motor will be used should also be taken into consideration. If the motor will be used in a high-speed application, a higher voltage may be necessary to achieve the desired speed.
7. Test and adjust: If possible, it is always a good idea to test the gear motor with different voltages to determine the optimal voltage for your specific application. This will ensure that the motor is operating at its best performance and efficiency. 6.What are the accessories and add-ons available for gear motors? 1. Mounting brackets: These are used to securely attach the gear motor to a surface or structure.
2. Couplings: Couplings are used to connect the gear motor to other components such as shafts or pulleys.
3. Gearboxes: Gearboxes can be added to gear motors to increase torque or change the speed of the output shaft.
4. Encoders: Encoders are sensors that can be added to gear motors to provide feedback on the speed and position of the output shaft.
5. Motor controllers: Motor controllers are electronic devices that can be used to control the speed and direction of the gear motor.
6. Cooling fans: For high-performance gear motors, cooling fans can be added to prevent overheating.
7. Limit switches: Limit switches can be added to gear motors to control the movement of the output shaft and prevent damage.
8. Brakes: Brakes can be added to gear motors to provide additional control and safety.
9. Lubrication systems: Lubrication systems can be added to gear motors to ensure smooth operation and extend the lifespan of the motor.
10. Power supplies: Depending on the type of gear motor, a power supply may be required to operate it.
11. Motor mounts: Motor mounts can be used to securely attach the gear motor to a surface or structure.
12. Gear motor controllers: These are specialized controllers designed specifically for gear motors, providing precise control and monitoring capabilities.
13. Gear motor enclosures: Enclosures can be added to gear motors to protect them from dust, moisture, and other environmental factors.
14. Gear motor adapters: Adapters can be used to connect gear motors to different types of shafts or components.
15. Gear motor repair kits: These kits contain replacement parts and tools for repairing and maintaining gear motors.
|