Founded in 2009,Mercury Motion specializes in high end micro motors, such as brushless motors, gear motors, stepper motors…etc.Especially the precision gear motors, we could design and produce all the gears and we have a full production line of CNC center .This combination makes us have the unique advantage of the gear motors industry. Our motors are widely used in cars, home appliances,medical equipment, electrical devices, ATMs and robots, etc.
Let’s continue! 1.How to determine the required power for a gear motor? 2.What materials are used in the construction of gear motors? 3.Is regular maintenance required for gear motors? 4.Can a gear motor be used in conjunction with other motor types? 5.How to reduce gear motor vibration? 6.What are the differences between helical, spur, and planetary gears in gear motors? 1.How to determine the required power for a gear motor? 1. Determine the load: The first step in determining the required power for a gear motor is to determine the load that the motor will be required to move. This can be done by calculating the weight of the load and the force required to move it.
2. Calculate the torque: Once the load is determined, the next step is to calculate the torque required to move the load. Torque is the rotational force required to move an object and is measured in Newton-meters (Nm). The formula for torque is T = F x r, where T is torque, F is force, and r is the radius of the gear.
3. Determine the speed: The speed at which the load needs to be moved is also an important factor in determining the required power for a gear motor. This can be calculated by dividing the distance the load needs to travel by the time it needs to be moved in.
4. Calculate the power: Once the torque and speed are determined, the required power can be calculated using the formula P = T x ω, where P is power, T is torque, and ω is the angular velocity (speed) of the gear.
5. Consider efficiency: It is important to consider the efficiency of the gear motor when calculating the required power. The efficiency of a gear motor is the ratio of output power to input power and is usually expressed as a percentage. Multiply the calculated power by the efficiency to get the actual power required for the gear motor.
6. Add a safety factor: It is recommended to add a safety factor of 10-20% to the calculated power to account for any unexpected variations in the load or operating conditions.
7. Choose the appropriate gear motor: Once the required power is determined, choose a gear motor that can provide the required power and torque at the desired speed. It is important to also consider the gear ratio, motor size, and voltage requirements when selecting a gear motor.
Note: It is always recommended to consult with a professional engineer or gear motor manufacturer for accurate calculations and selection of the appropriate gear motor for your specific application. 2.What materials are used in the construction of gear motors? The materials used in the construction of gear motors can vary depending on the specific type and application of the motor. However, some common materials that are often used include:
1. Metal alloys: Gear motors often use metal alloys such as steel, aluminum, and copper for their strength, durability, and conductivity.
2. Gears: The gears in gear motors are typically made of metal, such as steel or brass, to withstand the high torque and pressure required for efficient operation.
3. Bearings: Bearings are essential components in gear motors, and they are usually made of materials such as steel, bronze, or ceramic to reduce friction and support the rotating shaft.
4. Magnets: Permanent magnets, such as neodymium or ferrite, are commonly used in gear motors to create the magnetic field necessary for the motor to function.
5. Insulation materials: To prevent electrical shorts and ensure safe operation, gear motors often use insulation materials such as plastic, rubber, or ceramic.
6. Housing: The housing or casing of gear motors is typically made of metal or plastic to protect the internal components and provide structural support.
7. Wiring and connectors: The wiring and connectors used in gear motors are usually made of copper or other conductive materials to transmit electrical signals and power.
8. Lubricants: Gear motors require lubricants to reduce friction and wear between moving parts. Common lubricants used include oils, greases, and synthetic compounds.
9. Electronic components: Some gear motors may also include electronic components such as sensors, controllers, and circuit boards, which are typically made of plastic, ceramic, or metal.
10. Seals and gaskets: To prevent dust, moisture, and other contaminants from entering the motor, gear motors may use seals and gaskets made of rubber, silicone, or other materials. 3.Is regular maintenance required for gear motors? Yes, regular maintenance is required for gear motors to ensure their optimal performance and longevity. This includes cleaning, lubrication, and inspection of the gears, bearings, and other components. It is recommended to follow the manufacturer's maintenance schedule and guidelines for the specific gear motor model. Neglecting regular maintenance can lead to decreased efficiency, increased wear and tear, and potential breakdowns. 4.Can a gear motor be used in conjunction with other motor types? Yes, a gear motor can be used in conjunction with other motor types. For example, a gear motor can be used in conjunction with a stepper motor to provide precise positioning and control, or with a servo motor to increase torque and reduce speed. Additionally, gear motors can be used in conjunction with other types of motors in multi-stage systems to achieve different speed and torque requirements. 5.How to reduce gear motor vibration? 1. Balance the load: Make sure that the load on the gear motor is evenly distributed. An unbalanced load can cause excessive vibration.
2. Check for misalignment: Misalignment between the gear motor and the driven equipment can cause vibration. Make sure that the gear motor is properly aligned with the driven equipment.
3. Lubricate regularly: Proper lubrication is essential for reducing friction and vibration in gear motors. Make sure to use the recommended lubricant and follow the manufacturer's guidelines for lubrication intervals.
4. Check for wear and tear: Regularly inspect the gear motor for any signs of wear and tear, such as worn gears or bearings. Replace any damaged parts to prevent excessive vibration.
5. Use vibration dampening mounts: Vibration dampening mounts can help absorb and reduce the vibration from the gear motor. These mounts are typically made of rubber or other materials that can absorb vibrations.
6. Install a flexible coupling: A flexible coupling can help reduce vibration by allowing for some misalignment between the gear motor and the driven equipment.
7. Use a soft start or variable frequency drive: A soft start or variable frequency drive can help reduce the initial shock and vibration when the gear motor starts up.
8. Check for resonance: Resonance can occur when the natural frequency of the gear motor matches the frequency of the vibration. If resonance is an issue, consider changing the speed or adding a vibration damper.
9. Properly support the gear motor: Make sure that the gear motor is properly supported and secured to prevent excessive movement and vibration.
10. Consult a professional: If the vibration is excessive and cannot be reduced with these methods, it may be necessary to consult a professional for further troubleshooting and solutions. 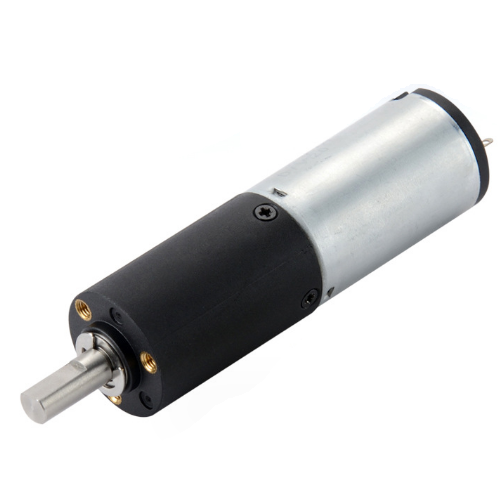
6.What are the differences between helical, spur, and planetary gears in gear motors? Helical, spur, and planetary gears are all types of gears commonly used in gear motors. Each type has its own unique design and characteristics, making them suitable for different applications. The main differences between these gears are their tooth profiles, load capacity, efficiency, and noise level.
1. Helical Gears:
- Tooth Profile: Helical gears have angled teeth that are cut at an angle to the gear axis. This helical shape allows for smoother and quieter operation compared to other gear types.
- Load Capacity: Helical gears have a higher load capacity than spur gears due to their larger contact area.
- Efficiency: Helical gears have a higher efficiency than spur gears due to their angled teeth, which allows for more teeth to be in contact at any given time.
- Noise Level: Helical gears produce less noise and vibration compared to spur gears, making them suitable for applications where noise is a concern.
2. Spur Gears:
- Tooth Profile: Spur gears have straight teeth that are parallel to the gear axis. This simple design makes them easy to manufacture and maintain.
- Load Capacity: Spur gears have a lower load capacity compared to helical gears due to their smaller contact area.
- Efficiency: Spur gears have a lower efficiency compared to helical gears due to their straight teeth, which results in less teeth in contact at any given time.
- Noise Level: Spur gears produce more noise and vibration compared to helical gears, making them less suitable for applications where noise is a concern.
3. Planetary Gears:
- Tooth Profile: Planetary gears have a unique design with a central gear (sun gear) surrounded by multiple smaller gears (planet gears) that rotate around it. This design allows for a compact and efficient gear system.
- Load Capacity: Planetary gears have a high load capacity due to the multiple contact points between the sun gear and planet gears.
- Efficiency: Planetary gears have a high efficiency due to the multiple contact points and the distribution of load among the planet gears.
- Noise Level: Planetary gears produce less noise and vibration compared to spur gears, making them suitable for applications where noise is a concern.
In summary, helical gears are known for their smooth and quiet operation, spur gears are simple and easy to manufacture, and planetary gears are compact and efficient. The choice of gear type depends on the specific requirements of the application.
|