Introduction
A brushless motor, also known as a BLDC (Brushless Direct Current) motor, is an electric motor that uses a permanent magnet rotor and a stator with electronically controlled windings to produce motion. Unlike traditional brushed motors, which use physical brushes to transfer electricity to the rotating armature, brushless motors use electronic commutation to achieve greater efficiency and reliability.
History of Brushless Motors
The development of brushless motors can be traced back to the 1960s with the introduction of solid-state electronics. However, it was not until the 1980s that these motors became commercially viable due to advances in power electronics and microcontrollers. Today, brushless motors are used in a variety of applications, from electric vehicles to industrial machinery.
How Does a Brushless Motor Work?
The basic principle of operation of a brushless motor involves the interaction between the stator and rotor. The stator is the stationary part of the motor that contains multiple windings or coils, while the rotor is the rotating part that contains permanent magnets.
When a DC current is applied to the coils of the stator, it creates a magnetic field that interacts with the permanent magnets on the rotor. This interaction generates torque, causing the rotor to rotate. The rotation of the rotor is then controlled by the electronic commutation of the stator windings, which is achieved through the use of sensors that detect the position of the rotor.
What is Six-Step Commutation?
Six-step commutation is a cost-effective means of electronic commutation, due to the simple and relatively inexpensive feedback and drive devices. In six-step commutation, only two out of the three Brushless DC Motor windings are used at a time. Steps are equivalent to 60 electrical degrees, so six steps makes a full, 360 degree rotation. One full 360 degree loop is able to control the current, due to the fact that there is only one current path. Six-step commutation is typically useful in applications requiring high speed and commutation frequencies. A six-step Brushless DC Motor usually has lower torque efficiency than a sine-wave commutated motor.
Physical Properties of a Brushless DC Motor
The Brushless DC Motor consists of a rotating rotor, Neodymium Iron Boron magnets, and a stator. Brushless DC Motors are considered to be an "inside-out" version of a Brush DC Motor; the commutator and brushes are nonexistent, and the windings are located externally, connected to the controller. There are typically two different construction types for the Brushless DC Motor: inrunner and outrunner configurations. The inrunner configuration consists of three stator windings located around the rotor, with permanent magnets as a part of the rotor. The outrunner has a reversed relationship between the magnets and the coils. The permanent magnets rotate inside a suspended rotor surrounding the core of the Brushless DC Motor.
Internally, a 3-phase motor can be configured to a "Wye" or "Delta" configuration. The primary advantage to the "Wye" configuration, also known as the Star configuration, is that the phase-to-neutral voltage is equal in all three legs. The arrangement is a parallel circuit in a shape of the letter Y, where all windings are connected at a central point, and power is applied to the remaining windings. 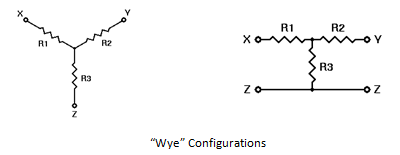
wye configuration The Delta configuration creates a triangle-like figure, making it a series circuit. This configuration applies power to each of the connections. 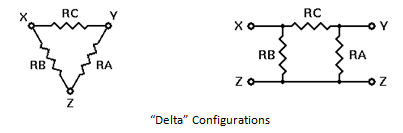
How is a Brushless DC Motor Controlled?
Brushless - Category - Controllers An electronic Brushless DC Controller (also known as a Driver, or Electronic Speed Controller), replaces the mechanical commutation system utilized by a Brush DC Motor, and is required by most Brushless DC Motors to operate. In a Brushless DC Motor controller, either a Hall Effect Sensor or Back EMF (Electromotive Force) is used to identify the position of the rotor. Understanding the orientation of the rotor is crucial to operating the Brushless DC Motor.
The Hall Effect uses three hall sensors within the Brushless DC Motor to help detect the position of the rotor. This method is primarily used in speed detection, positioning, current sensing, and proximity switching. The magnetic field changes in response to the transducer that varies its output voltage. Feedback is created by directly returning a voltage, because the sensor operates as an analogue transducer. The distance between the Hall plate and a known magnetic field can be determined with a group of sensors, and the relative position of the magnet can be deduced. A Hall sensor can act as an on/off switch in a digital mode when combined with circuitry.
Back EMF, also known as the Counter-Electromotive Force, is caused by a changing electromagnetic field. In a Brushless DC Motor, back EMF is a voltage that occurs where there is motion between the external magnetic field and the armature of the motor. In other words, the voltage is developed in an inductor by an alternating or pulsating current. The polarity of the voltage is constantly the reverse of the input voltage. This method is commonly used to measure the position and speed of the Brushless DC Motor indirectly, and due to the lack of Hall Sensors within the controller, these are often referred to as sensorless controllers.
Optical Encoders can also be added to the Brushless DC Motor, allowing both direction and speed to be determined. More precise applications may use Optical Encoders with a third index signal, to determine pulse per revolution.
Benefits of Brushless Motors
One of the main advantages of brushless motors over traditional brushed motors is their higher efficiency. The absence of brushes eliminates the friction and sparking associated with traditional motors, resulting in less energy loss and heat generation. This makes brushless motors more reliable and longer-lasting.
Additionally, brushless motors have a higher power-to-weight ratio, making them ideal for applications where space and weight are at a premium. They are also more compact and have a higher power output compared to traditional motors.
Types of Brushless Motors
There are two main types of brushless motors - outrunner and inrunner. Outrunner motors have a stationary outer shell and a rotating inner shaft, while inrunner motors have a rotating outer shell and a stationary inner shaft.
Outrunner motors are commonly used in applications that require high torque, such as electric bikes and drones, while inrunner motors are typically used in smaller, high-speed applications such as computer fans and RC cars. 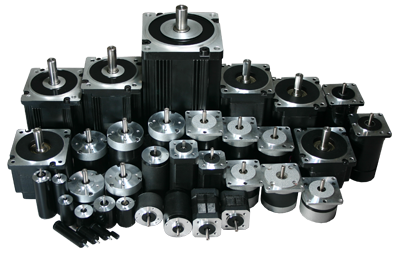
Applications of Brushless Motors
The high efficiency, compact size, and reliability of brushless motors make them suitable for a wide range of applications. Some common uses of brushless motors include:
- Electric vehicles: Brushless motors are used in electric and hybrid vehicles for their efficiency and ability to deliver high torque at low speeds.
- Industrial machinery: Brushless motors are used in various industrial equipment, such as pumps, compressors, and machine tools, for their high power output and precise control.
- Consumer electronics: Brushless motors are used in various devices, including hairdryers, electric toothbrushes, and fans, as they are compact, quiet, and have a long lifespan.
- Aerospace and defense: Brushless motors are used in drones, missiles, and military equipment for their high power output, compact size, and reliability.
Challenges for Brushless Motors
Despite their many advantages, brushless motors also have some challenges to consider. One of the main challenges is cost. The technology and equipment required to manufacture brushless motors can be expensive, making them more expensive compared to traditional brushed motors. However, as technology advances and demand increases, the cost of brushless motors is expected to decrease.
Another challenge is the need for electronic control. The electronic commutation of brushless motors requires more complex control systems compared to traditional motors, making them more challenging to design and maintain.
Troubleshooting a Brushless DC Motor
Problem: The Brushless DC Motor is running incorrectly, or stops running. Solution: A Brushless DC Motor having difficulty operating could indicate that the Hall Sensors are bad. To check, use a resistor to pull up each Hall to 5 volts, and check each Hall with an oscilloscope while spinning the shaft.
Repeat this process for each individual Hall. When spinning the shaft manually, a low and high signal should appear on the scope. Keep in mind the importance of what value is used for the resistance; this depends on the amount of current the Hall sensors can withstand.
If this test demonstrates that the Hall Sensors are working correctly, the next step is to check the phases of the Brushless DC Motor. Hook up the Brushless DC Motor to a controller. With an oscilloscope, check each phase to see if a switching signal is present. If the phases do not pose a problem, this may indicate a bearing problem, or internal shorts. If these techniques do not seem to explain why the Brushless DC Motor is working improperly, the purchase of a new Brushless DC Motor should be considered.
Conclusion
Brushless motors have revolutionized the world of electric motors, offering higher efficiency, compact size, and reliability in a wide range of applications. As technology continues to advance, brushless motors are expected to become more affordable and accessible, making them even more prevalent in various industries. It is safe to say that brushless motors have a bright future ahead as a key component in the development of more efficient and sustainable technologies.
|